Making the right decisions about what kind of new lab furniture to specify for your existing laboratory, renovated lab space or all new, purpose-built lab facility is both exciting and challenging. You want to make the right investment choices — because the decision you make today will have long-term consequences for years to come.
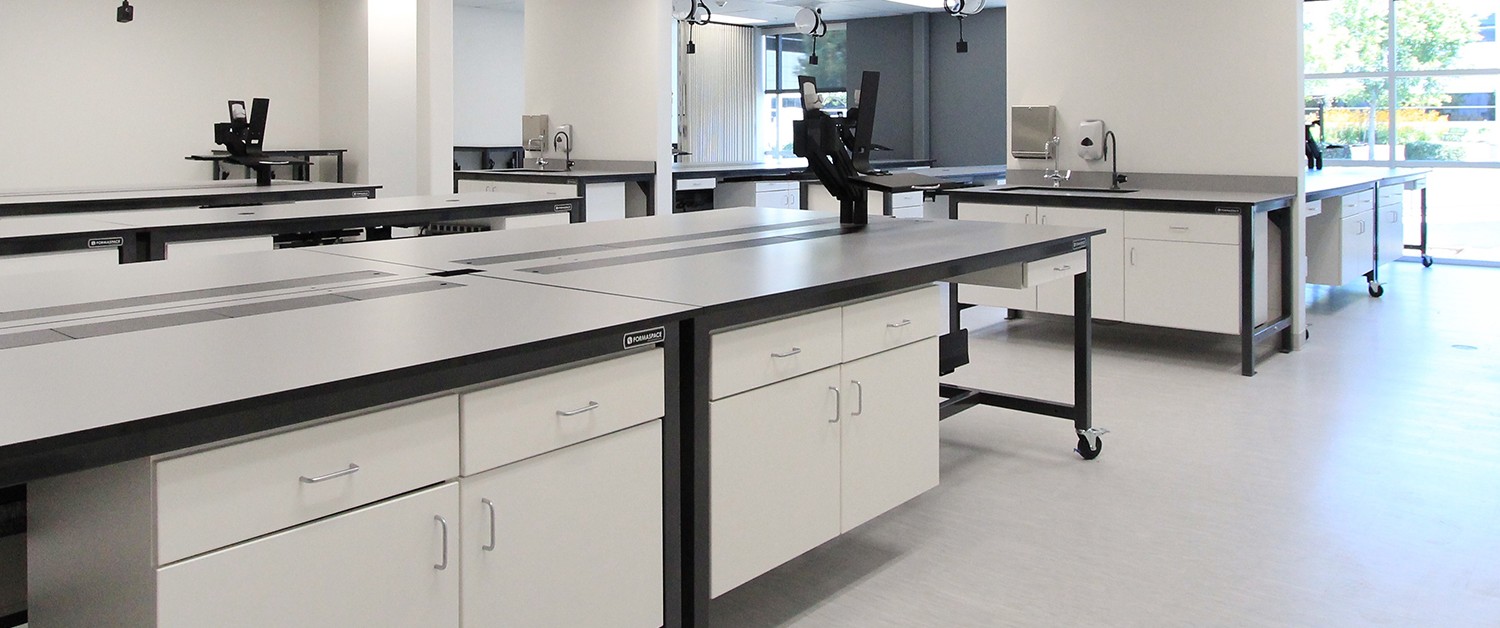
In our experience, clients facing the challenge of selecting laboratory furniture for the first time can become overwhelmed by all the choices and don’t know where to begin.
That’s why we prepared a checklist of twelve different design considerations you should take into account when searching for laboratory furniture. This approach will help you identify questions that you may not have thought about before, as well as pinpoint areas where you will need to focus your research in order to gather the final design requirements.
Once you have this information in hand, you’ll be able to work with one of our Formaspace Design Consultants to come up with an optimal design for your laboratory furniture that works best to satisfy your unique set of design requirements.
Let’s get started!
Consideration 1: Which Category of Laboratory?
Answering this question should be easy unless you are kitting out a laboratory on spec, attracting clients to use the facility (That will take more market research!)
Typical lab categories include:
- Educational and teaching classrooms
- Manufacturing and semiconductor production
- Electronics and testing
- Healthcare medical testing
- Biomedical research and manufacturing, including healthcare products, pharmaceuticals, and medical devices
- Chemical, oil and gas refining, manufacturing and testing
- Radiological research
…and many more.
Consideration 2: What Regulatory Regime Applies?
Nearly every laboratory falls under one or more sets of regulatory guidelines, whether it’s FDA regulated Current Good Manufacturing Practices (cGMP), ISO 14644 cleanroom standards, mandates issued by credentialing authorities for higher education institutions, OSHA safety standards to protect workers or EPA regulations to protect the environment.
To help you identify what regulatory rules apply, review the lab category identified in the first step. Then ask yourself if you are selling manufactured goods; if so, which regulatory agencies govern sale and trade in this industry sector?
Then determine which state, federal or international standards will apply to worker safety, standards for handling and transporting dangerous materials, environmental pollution standards, and so forth.
You may discover that specific regulations will dictate what kind of laboratory furniture you can use in your facility. For example, regulations covering food manufacturing laboratories may require laboratory furniture with stainless steel surfaces.
Consideration 3: Wet Lab versus Dry Lab
One of the first questions that laboratory designers and architects want to know when specifying laboratory furniture is whether the liquid chemicals will be used in the lab. These so-called ‘wet labs’ generally have very specific design requirements, such as the need for chemical resistant surfaces, conveniently accessible built-in wet sinks — as well as all the requisite plumbing required. Lab workers working in a wet lab environment will need extra safety equipment, such as eyewash stations. Emergency showers may also be required, as well as built-in fume hoods to protect workers from exposure to dangerous chemicals.
In contrast to wet labs, dry labs are characterized as facilities that work directly with very small volumes of dry chemicals on a very limited basis, if at all. In fact, the trend for dry laboratories is that they have become more like information technology laboratories that are populated with expensive electronic gear and robust networks. In some cases, ultra-sensitive lab equipment will require vibration isolation and perhaps a purified air supply to prevent contamination of instruments and samples (see the section on cleanrooms below).
An important design consideration for dry labs is to recognize that test equipment used in these types of facilities changes rapidly as technology advances. Therefore, the laboratory furniture you specify today needs to be flexible, modular and reconfigurable in order to be able to make changes as new uses arise tomorrow.
Consideration 4: Electro-Static Discharge Requirements
Laboratories supporting electronic component manufacturing and repair, such as chip manufacturing or computer assembly laboratories, need to design their equipment to prevent possible electrostatic discharge, which can ruin sensitive microelectronics.
If you need to assemble, test, inspect, ship and/or package electronic components that are vulnerable to the effects of static charge, Formaspace can help. We have a complete line of workstations and packing stations with work surfaces constructed out of special materials that provide built-in electrostatic discharge protected areas (EPAs). Choosing laboratory furniture with built-in anti-static protection is the way to go if you have this requirement.
Consideration 5: Laboratory Heat or Chemical Exposure to Surfaces
It’s important to try to identify which chemicals (if any) you will be using in the laboratory during its lifetime. What about high-temperature exposures which may occur when placing very hot objects on the work surface?
Having this information on hand will make it easier to determine which materials to use in constructing the work surfaces on your laboratory furniture.
Once you have an idea which chemicals and heat exposures it exposures you’re likely to expect, refer to our article on choosing the right countertop surface for different chemical and heat exposures.
Consideration 6: Cleanroom and / or Fume Hood Requirements
Does your laboratory need to incorporate a cleanroom system to protect sensitive equipment and samples from microscopic contamination? What about protecting workers from chemical exposure? Will you need to build in a fume hood solution?
If the answer is yes to either or both of these questions, we have prepared additional information for architects designing cleanroom spaces. This article will help orient you in the different considerations necessary for specifying laboratory furniture, such as layouts design considerations to increase airflow and furniture material selection to prevent contamination.
Consideration 7: Laboratory Funding Model
Let’s shift gears for a moment, and talk about some financial concerns.
In the past, laboratories were typically designed with a lifetime of 20 to 30 years or more in mind.
Now the situation is different. Today’s grant-supported research is often subject to very short-term funding cycles, and industry-based research projects are often tied to short, rapid product development cycles as well.
Increasingly, the short funding cycles dictate that more and more laboratories are constructed, used, and decommissioned or re-purposed for different projects within a matter of a few years.
If you’re funding or development cycle dictates a shorter laboratory lifetime, you should consider using modular laboratory furniture. This can be re-purposed easily for the next tenant or project use. It can also be easily disassembled and transported to a new location.
Consideration 8: Real Estate Considerations
The real estate market can also have an impact on the selection of laboratory furniture.
As the healthcare and biotech market expand in certain cities, such as San Francisco and Boston, there are spot shortages of laboratory space for lease, and they may be expensive. As a result, many lab planners are looking for suburban locations.
To keep up with demand, it’s not uncommon for developers to convert existing spaces from their original uses into laboratory facilities.
As with brand new construction, heavily remodeled facilities can use the more modern modular lab furniture designs, which can be reconfigured over time to keep up with changes in the laboratory technology — unlike built-in casework, which is our next consideration topic.
Consideration 9: Modular Lab Furniture Versus Casework
The term casework refers to the style of laboratory furniture that’s permanently built-in, e.g. attached to the walls. It’s very difficult to remodel this style of laboratory furniture should your needs change. In contrast, modular furniture can be assembled on-site without a carpenter; reconfigured easily over time, or transported for use in other location, if needed.
Generally speaking, unless you are renovating or updating an existing, historic design laboratory with traditional built-in casework design, we recommend using modular furniture, which can be adapted easily as your needs change.
Check out our article on the cost of modular furniture versus casework; you’ll be pleasantly surprised how modular lab furniture is often the budget friendly choice, as it can be manufactured more quickly, transported easily, and installed in less time than traditional casework.
Consideration 10: Can Your Lab Furniture Be Future Proof?
If you look back over last 20 years in laboratory design, it would have been hard to predict all the changes that we’ve seen. Test equipment has gotten much smaller, advanced laboratory techniques like genomic research have become mainstream, and research working styles have become more collaborative.
All of these elements have contributed toward making laboratory design more open and flexible.
What will the next 20 years bring? Probably the only predictable answer is more change. That’s another reason to consider modular furniture designed for your laboratory, which you can reconfigure as your needs change over time.
Consideration 11: Maximizing Productivity in Limited Spaces
Formaspace not only manufacturers our own furniture here in Austin, Texas, but we also provide consulting services to make your operations more efficient. One such service we offer is space planning.
Based on our experience working with many laboratory clients, we recommend you evaluate your space planning needs carefully.
For example, we have found quite a few situations where clients come to us with expansion plans because they feel they are running out of laboratory space.
However, when we make an on-site client visit, we sometimes discover that the need to expand to a larger facility may not be necessary at all, or can at least be postponed for several years.
Sometimes all that is needed is to incorporate custom-designed storage into the existing lab facility, such as vertical storage solutions or other space-saving components. In one example, this saved a Formaspace pharma client a million dollars in labor costs.
Consideration 12: Make the Most of Your Budget by Considering Total Costs
If you have a budget identified for your project, you will want to spend it wisely.
Often renovation or construction projects have to be started and completed within a predictable window time, otherwise, costs penalties and disruption and spiral out of control.
Time is money, as they say.
We’ve heard stories throughout the laboratory industry about how projects can get badly off track, particularly when it comes to quality and delivery issues.
Unlike other vendors who resell laboratory furniture made overseas in China (that can take weeks if not months to be delivered), Formaspace is different. We make all our lab furniture here in Austin, Texas — at our factory headquarters — using all locally-sourced materials, including high-quality, American-made steel.
There is no ‘passing-the-buck’ here at Formaspace. You receive a dedicated, single point of contact that is located in the same building as our factory — just steps away from where your laboratory furniture is manufactured. Your dedicated Design Consultant will make sure any issues or changes needed are resolved quickly and to your satisfaction.
Because all our furniture is built here in Texas, it can be delivered to you quickly. We ship over 99% of our orders on time — and 67% of our orders are shipped out earlier than the date we promised.
What about durability? It’s important to protect your investment in laboratory furniture. Formaspace furniture is built tough. We design all our furniture to withstand the rigors of use in a factory, even if it only gets used gently in a laboratory. All our furniture is guaranteed for a full 12 years, even if you use it 24 hours a day in a factory setting.
Formaspace is the Place to Start for Laboratory Furniture
We hope these twelve different laboratory considerations can guide you during your laboratory furniture selection process.
The Design Consultants here at Formaspace are ready to help.
When you’re ready to talk about making an investment in your lab furniture, just drop us a line by email, use the contact form below, or give us a call at 800.251.1505.
You’ll be glad you did.