Creating a Safety Culture in the Laboratory
Did safety culture take a back seat in your lab during the pandemic?
It’s quite possible.
But now is the time to set things right.
After several years of the pandemic, we need to redouble our efforts.
This means helping new hires or students who may not have had good hands-on lab training during the pandemic become champions who practice and advocate for increased lab safety.
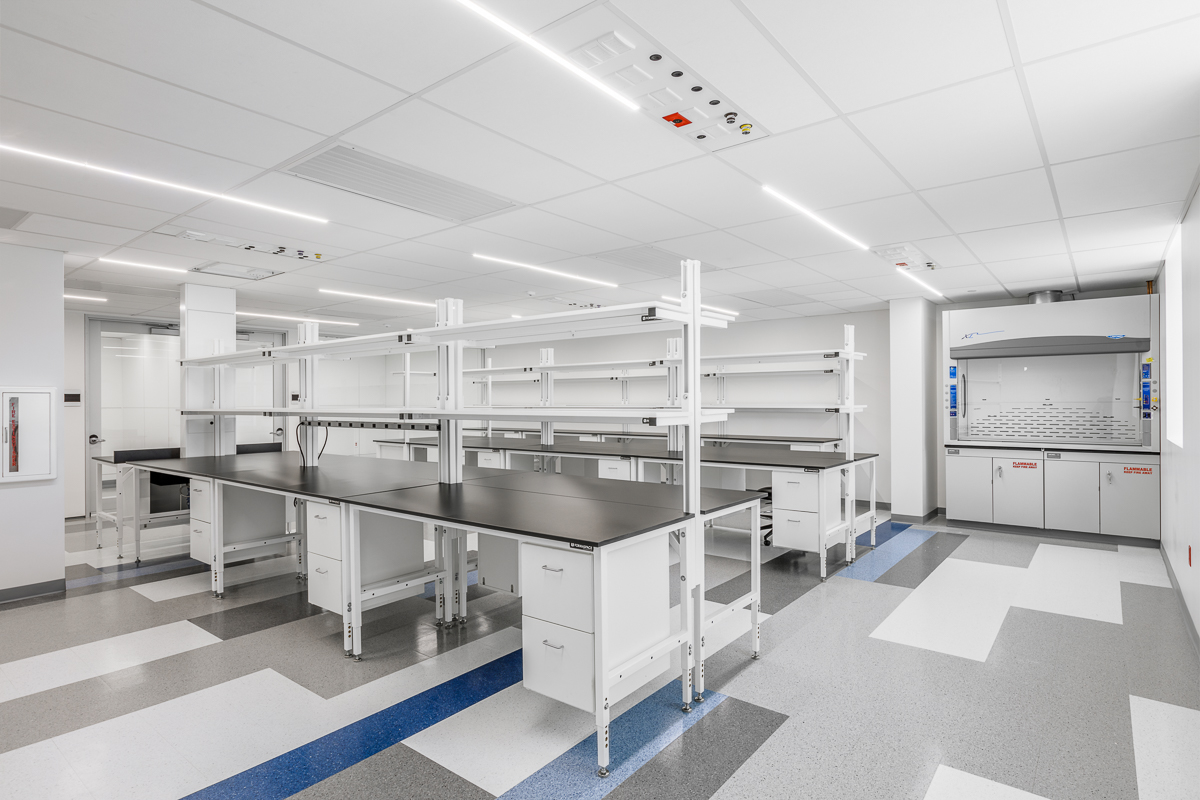
Veteran lab workers and even PIs who may have come to rely on ‘ad hoc’ processes and other non-standard protocols during the Covid era will also benefit from a refresher course on lab safety.
How do we get started?
In most lab environments, we need to start at the top.
Senior management needs to make it crystal clear that Lab Safety is Job One!
According to lab safety expert Dr. Jim Kaufmann, a former Dow employee who has dedicated his life to promoting lab safety at the Laboratory Safety Institute (LSI), there are four key elements of successful lab safety culture that the top leadership of the organization needs to adopt, promote, and where necessary, enforce them:
· The 4 C’s of Lab Safety
1. Choices
According to Kaufmann, we have to make a conscious choice to commit to laboratory safety, starting with top management.
2. Consequences
There need to be serious consequences for choosing not to follow safety guidelines, including termination or expulsion for not following the rules.
3. Convincing
Leadership must be proactive and work to convince staff members they are serious about lab safety.
4. Caring
Ultimately, lab safety is about caring – adhering to proper safety protocols can help save a life, whether it’s yours or your colleagues.
A Review of the Leading Causes of Laboratory Accidents
Why is lab safety so important?
A quick view of the latest available accident data from the Bureau of Labors Statistics (BLS) shows that lab accidents continue to happen at a high rate.
Incidence rates in 2020 of nonfatal occupational injuries and illnesses by select industry and case types (per 100 full-time workers). Note: excludes fatal injuries.
Industry | NAICS code | Total recordable cases | Cases with days away from work | Cases with days of job transfer or restriction | Other recordable cases |
Testing laboratories | 54138 | 0.6 | 0.1 | 0.2 | 0.3 |
Other scientific and technical consulting services | 54169 | 1.1 | 0.5 | – | 0.3 |
All other professional, scientific, and technical services | 54199 | 0.6 | 0.3 | 0.1 | – |
Medical and diagnostic laboratories | 6215 | 2 | 0.7 | 0.2 | 1.1 |
Here we can see that within the laboratory category, Medical and diagnostic laboratories had an even higher number of cases – with 2% of workers having a recordable injury or illness.
One possible explanation for this is that medical and diagnostics labs generally fall into the “wet lab” category, which has a greater potential for lab accidents.
To this point, the CDC publishes its Morbidity and Mortality Weekly Report (MMWR), which documents lab accidents, injuries, and illnesses.
According to the MMWR, bacterial and viral infections are a major concern in diagnostic labs, with bacteria causing more than 40% of laboratory-acquired infections (LAIs). Viral infections are also higher among lab workers – Hepatitis B infections are between 2 and 4 times higher than among the general public.
How do these infections occur?
The CDC has identified five leading causes of laboratory-acquired infections:
- Accidental inoculation by syringe needles or contaminated sharps.
- Spills and splashes on skin or mucous membranes.
- Ingestion or exposure by mouth pipetting or touching the mouse or eyes with fingers or contaminated objects.
- Laboratory research activities involving animal bites or scratches.
- Inhalation of infectious aerosols.
Of course, there are many other safety concerns in laboratories.
To get a more nuanced view of laboratory accident rates, it’s useful to turn to specialized reports that track accident and fatality incidents within laboratories.
One important resource is the Laboratory Safety Institute’s Dr. Jim Kaufman (who we introduced earlier). Kaufman’s organization has published a three-volume series of books called Learning by Accident that painstakingly documents over 1,500 laboratory accidents.
What is especially useful about this highly-recommended resource is that it cross-references each accident by specific chemicals, processes, equipment, or procedures, which means that you can look up individual items such as “hydrochloric acid,” or “protecting equipment, lack of” and read the relevant passages documenting the tragic consequences of an accident related to the topic.
Another organization that investigates accidents in laboratories (and industrial facilities) is the U.S. Chemical Safety and Hazard Investigation Board (CSB).
During the late 2000s and early 2010s, the CSB began an in-depth investigation to learn the root cause of a series of fatal and debilitating accidents taking place at several American university and college laboratories, including a fire that killed a UCLA graduate student and maimed a graduate student at Texas Tech.
After an exhausting investigation, the CSB created a video “Experimenting with Danger” that documents the important “lessons learned” from the lethal laboratory accidents at Yale, UCLA, Dartmouth, and Texas Tech.
We’ll review the CSB’s specific lab safety recommendations next.
Lab Safety Planning and Training
What’s the right way to establish and maintain a strong safety culture in your laboratory?
One suggestion is to follow the four recommendations put forth by the CSB after it investigated serious and fatal accidents at academic laboratories.
· Create Written Protocols and Training Programs
Every lab environment is different. That’s why it’s important to evaluate each of the specific hazards found in your lab (as well as anticipate future lab activities and potential hazards) and then develop specific written protocols documenting safety procedures – as well as creating detailed, written training materials for conducting on-site safety classes.
· Address Physical Hazards in the Laboratory
It’s possible to get tunnel vision when looking at lab safety risks; for example, you might become too focused on the risks of handling a specific chemical under the fume hood while ignoring other potential risks in the lab, such as trip hazards from storing items out in the open or wet floors that can cause slip and falls.
Dr. Kaufman illustrates this point: he has seen cases where lab workers collect liquid directly from the newer high-pressure liquid chromatography (HPLC) test equipment by flushing directly into an open container – risking a liquid spill that could lead to a slip and fall – or exposure to dangerous, noxious gases collecting outside the fume hood.
Another question to ask is how will containers and tanks be physically moved within the lab? For example, moving an open container of liquid nitrogen in an elevator is a serious risk to lab personnel if the elevator gets stuck between floors – possibly causing suffocation.
· Safety Personnel Must Report Directly to Senior Leadership
Junior staff can be intimidated when they see more senior workers take safety shortcuts or elect to proceed with dangerous, risky protocols.
That’s why the CSB recommends that safety personnel report directly to senior officials who have the authority to oversee research laboratories and implement improvements.
As we stated at the beginning, senior leadership needs to “own” safety and communicate its importance. One suggestion from Dr. Kaufman is to ask every employee and prospective hire this question: “What have you done in the past to help contribute more effectively to a lab safety program?”
· Document all Accidents/Near-Misses and Communicate Valuable Lessons Learned
The CSB’s final recommendation is that it’s crucial to carefully document all laboratory incidents, whether they result in fatal or life-threatening accidents or only “near-misses.”
Collecting this information and communicating it helps to build up our knowledge of “lessons learned” and avoid repeating the mistakes of the past.
The LSI goes one step further, recommending that you need to reward good lab safety behavior by recognizing the achievements of lab workers by giving out safety leadership awards.
The Importance of Well Designed and Equipped Lab Environments
How do you go about designing and building a safe, effective, and productive laboratory environment?
Here are a couple of high-level recommendations to keep you on the right track.
· Selecting a Safety and Compliance Lead in Lab Facility Planning and Operations
When it comes to designing a new laboratory or making renovations to an existing one, you need to identify a lab safety specialist who will be able to make informed assessments of the space and layout requirements, evaluate the architect’s programming recommendations, review detailed working blueprints, and help keep the project on track in accordance with regulatory compliance requirements.
It’s also important that this person (and the team) don’t fall prey to pressure to “value engineer” safety measures and cut them out of the project.
· Use Proper Space Planning to Create Safer Laboratory Conditions
Having a lab safety specialist on board during the early planning stages of a project can help avoid common errors that can undermine lab safety efforts.
For example, it’s not a good idea to mix eating and drinking with lab operations. Make sure there is a clear policy on this, and help the situation by providing suitable eating facilities away from the lab where personnel can change out of any protective equipment (including lab coats) to avoid cross-contamination when having a break time or lunch.
Similarly, avoid placing fume hoods near busy doors and corridors or other places where people will congregate. With doors opening and closing, there is a greater chance that fumes will become misdirected away from the vents, posing a health risk not only to members of the lab team but to those within the building at large.
Speaking of crowding, cramming too many people and too much equipment into a limited space is a recipe for courting disaster. Avoid trip hazards and other accidents by ensuring that spaces are kept clear. Research all the storage requirements for the lab, including test materials, chemicals, lab equipment, and workbench spaces, while ensuring that there is adequate space by providing a sufficient quantity of storage spaces, biosafety cabinets, waste disposal facilities, etc.
A place for everything and everything in its place should be your motto.
Remember: a clean, well-lit, and ergonomic laboratory will have fewer accidents.
As you perform each experiment, consider what could go wrong.
- Is the personal protective equipment stored logically in a way that reminds you to use it properly?
- Do you need to install additional splash guards to protect your face, eyes, and skin from accidental exposure?
- Is the fume hood certified for using the chemicals you are currently using?
· Ensure that Safety Equipment is Present, Tested, and Working
Finally, be alert for the presence and condition of safety equipment, including emergency showers (with privacy curtains), eyewash stations, electric shutoff panels, and fire safety equipment (such as fire blankets to extinguish flames on your person.)
Over time, there is a tendency to let this equipment fall into disuse, either by not performing regular testing (to see if a shower works, for example) or by treating it as unused space where overflow items, such as storage boxes or carts, can be stowed.
Make testing and verifying the condition of this equipment part of your regular safety inspections so that you can be certain it will be ready to assist you in an emergency.
Formaspace is Your Laboratory Safety Partner
When it comes to modern laboratories, if you can imagine it, we can build it – here at our factory headquarters in Austin, Texas.
Why not contact your Formaspace Design Consultant today and see how we can work together to make your next laboratory project a success?