Why Pursue Flexible Manufacturing?
2020 and 2021 have been challenging years for manufacturing companies.
Thanks to the coronavirus pandemic, raw material shortages have torn through global supply chains – and it remains difficult to find enough highly skilled workers for today’s high-tech manufacturing facilities.
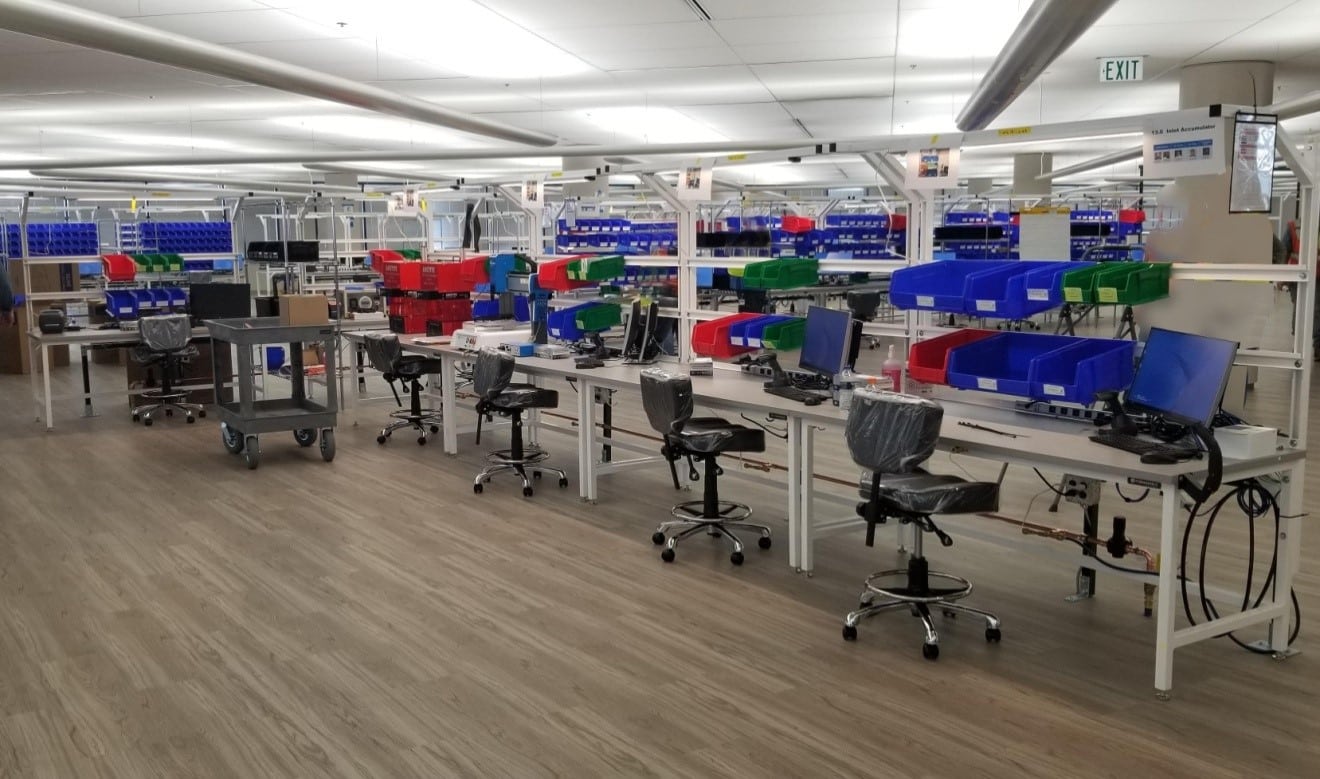
Given these challenges, manufacturing executives keep asking, “how can we make our factory is more flexible?”
Let’s take a moment to expand a bit on what managers might hope to achieve by creating flexible factories.
Here are some of the top reasons:
· Outflank the Competition with New and Varied Products
A flexible production system can help companies introduce highly differentiated products before their competitors do. Flexible manufacturing can also help create a wider product range to keep customers “within the family” and in and out of the hands of the competition.
· Match Production Levels with Changing Customer Demand
Flexible factories can respond quickly to rapid changes in customer demand by either increasing or decreasing the rate of production.
· Reduce on Hand Inventories (and Capital Carrying Costs)
Factories that can start and stop production quickly can avoid relying solely on long production runs – reducing inventory buildup and high capital carrying costs.
· Successfully Navigate Supply Chain Disruptions
In an ideal world, flexible factories can continue producing goods despite supply chain disruptions and production shutdowns, either by switching to alternative raw materials or parts or by quickly switching to the production of other products.
· Serve Profitable Custom or Niche Markets
Manufacturing custom products to meet the unique needs of customers can be profitable if done efficiently at scale – without disrupting other production requirements. Serving long-tail markets with niche products can also be very profitable if the manufacturing facility can handle short production runs efficiently.
· Revive Sales of Long-Established Products
Flexible factories can support sales campaigns that “juice” up demand for long-established products, for example, by producing limited edition production runs, often featuring unique colors or materials.
· Offer Unique Products for Each Sales Channel
Flexible factories can also produce differentiated products sold at different price points to address luxury and/or mass markets; geographical markets with unique requirements (such as RHD vehicles); or specific sales channels (such as wholesale, direct, retail, or e-commerce).
Requirement 1: Determine Your Flexible Manufacturing Goals
Now comes one of the hardest steps in pursuing a flexible manufacturing philosophy – identifying your key goals/justifications for creating a flexible factory – as well as how you plan to measure whether the program is ultimately successful or not.
“Why is this a difficult process?” you might ask.
As we’ll see in a second, there are a lot of competing ideas about what makes a successful flexible factory.
Here are just a few of the key goals that you could focus on:
· Goal A: Respond to Customer Orders Quickly by Switching From Producing One Product to Another
· Goal B: Create a Wide Product Range based on a Core Product Competency
· Goal C: Create a Wide Product Range with Very Different Product Offerings
· Goal D: Introduce New All Products to the Range without Disruption
· Goal E: Specialize in High Volume Production of Individually Customized Products
After reading this list, you might say, “Great, I’ll take them all.”
But unfortunately, pursuing all these goals at one time will NOT lead to success.
It’s far better to make a careful assessment of your requirements and identify one crystal-clear goal that you can implement across the organization – starting (as we’ll see in the next section) with your workforce.
Requirement 2: Recruit, Train, and Retain a Flexible Workforce
What’s the most important investment you can make to create a successful flexible factory?
Is it investing in new industry 4.0 infrastructure or smart factory software?
The answer is no.
People are your most important investment.
· A Skilled Workforce is the Most Important Ingredient for Flexible Factory Success
Operations and supply chain management expert David M. Upton really makes this clear in his classic study “What Really Makes Factories Flexible?” in which he takes an in-depth look at flexible production in the paper industry. He found that managers said 40% of their flexible factory initiatives were unsuccessful or disappointing. However, among successful projects, an experienced workforce that was trained to work toward specific flexibility was key – far more important than investing in software solutions or other technology.
· Ways to Overcome Manufacturing Worker Shortages
Of course, this poses a problem. As manufacturing companies are all too aware, skilled worker shortages are hitting the manufacturing industry especially hard.
A joint study by Deloitte and The Manufacturing Institute surveyed over 800 companies and found we could have 2.1 million unfilled manufacturing jobs by 2030.
What can we do about it? MIT proposed that we pursue more apprentice training programs along the lines of Germany. Meanwhile, the Manufacturing Institute (sponsor of Manufacturing Day) has created a #CreatorsWanted marketing campaign to drum up interest in manufacturing careers. (And if that isn’t enough, they suggest we consider giving felons a second chance in the job market.)
What can you do?
Sponsor local school programs by funding a Makerspace in your local high school or community college. Offer one-on-one mentoring programs for students and young graduates. Make your workplace friendly to those who are unfamiliar with factory settings; set a good example with a clean, attractive, and ergonomic workplace (this will help with worker retention as well).
· Double Down on Clear Worker Training to Meet Clear Flexibility Goals
The study by Upton mentioned above really emphasizes the importance of effective worker training. Workers who clearly understood management’s goals for achieving success in flexible production methods performed the best in achieving those goals.
Requirement 3: Implement Flexible Product Design
· Product Design Engineers Belong on the Factory Floor
Product designers and engineers need to be co-located on the factory floor with production managers, not in an office far away. (The only exception to this rule is when product designers leave the facility – to meet with end-users and suppliers, which they should do often.)
· Makerspaces Can Help Encourage Creative Solutions
Building a product development lab or makerspace adjacent to the production line is a good idea to allow engineers and production teams to work together to solve problems
· Design for Manufacturing (DFM) is More Important than Ever
Building products that are designed to be easily manufactured in the first place (using techniques as top-down assembly design) is an important foundation for flexible production. Many industries also design their products around core platforms that can be customized easily to extend the product range.
· Digital Twin Prototyping and Visualization Tools Can Help Identify Problems Early
Digital Twin Prototyping, a spin-off of CAD and Virtual Reality, is gaining ground in product prototyping. By building a fully digital version of a product (and the production line needed to build it), designers and production engineers can spot problems early before investing in tooling.
· Create Multiple Concepts Based on Heterogeneous Build Philosophies & Second Supply Chain Sources
Product engineers are now commonly creating multiple design concepts to meet their design specifications; e.g. may create a cast metal design, an additive manufacturing (3D printing) design, or a carbon-reinforced plastic design – all of which can be considered for production depending on the volumes required, speed to first production, unit cost, and availability of raw materials. Engineers are also designing multiple versions of products with key components supplied by secondary supply chain sources – to avoid production shutdowns in case of shortages.
· Coming Soon: Deconstruction/Recycling Requirements for Sustainability
Product designers should also be aware of new flexibility requirements coming down the line, particularly for products destined for sale in the EU, which will likely increase demands on manufacturers to make their products even more readily recyclable. See this YouTube video of the 2021 Munich Auto Show for example of this on the BMW stand, where a new prototype car features parts made of single materials to facilitate recycling at the end of the product life.
Requirement 4: Create Flexible Production Layouts using Prototypes
· Identify What Success Means, and How You Can Measure It
How will you measure success? Our first requirement was to determine our flexible manufacturing goals. With that information in hand, now it’s time to translate that flexibility goal into something measurable from a production point of view. Examples include production changeover in X hours, introduce a new product on the production line in Y days, etc. Remember, if you don’t set a metric now, you can’t measure success later.
· Use Prototyping to Test Flexible Production Layouts
Many manufacturing companies seeking to create more flexible production lines find success in breaking the problem into smaller pieces.
For example, increasing the number of products output by the factory might create unexpected bottlenecks in the packing and shipping department or in material handling operations (due to a wider range of incoming parts and raw materials).
You can address these issues by creating prototype production layouts in which you experiment with different layouts (of picking stations or warehousing layouts, for example).
Formaspace can help by building prototype production line material handling systems that you can test on a parallel production line – so you can optimize it in an A-B test before installing it factory-wide.
· Use Digital Twins to Evaluate Capital Intensive Production Lines
Digital Twin technology is not just for product design engineers, it’s just as powerful a solution for production engineers — and assembly line workers who can use it to learn new flexible production methods as well as critique it based on their hands-on, real-world experience on the factory floor.
Digital Twins are especially useful for complex and/or expensive production lines where an investment in tooling might cost millions of dollars. Identifying any issues before writing a check can be a career-saving move.
Requirement 5: Use Flexible Tooling and Production Methods
· Think People First
We can’t emphasize this enough. Workers are the most flexible production tool in your arsenal if you manage and lead them effectively. Taking a worker-first approach will help you achieve flexible factory success.
· Consider Non-Traditional Production Methods, Especially for Short Runs
As we mentioned above in the section on Product Design, there are exciting new materials and production techniques that can help companies meet their goals for flexible manufacturing. Additive manufacturing (3D printing), fully automated CAM machining systems, and molded resins reinforced with carbon fiber give flexible factories many new viable options for faster production changeovers.
· Efficiency Doesn’t Have to Be Expensive
Another misconception about flexible factories is that every investment has to be expensive. On the contrary, many improvements involve better organization, with cleaner layouts, simpler material handling pathways, and other production methods first proposed by Toyota, including visual indicators (Kanban) that help speed up production.
· Invest in Automation to Work with Human Employees
As we keep repeating, your human workforce is the most important. Avoid an adversarial approach of looking for ways to replace them with robots. Instead, think about using collaborative robots (Cobots), mobile manipulators, and other robotic systems that can be easily reprogrammed to perform different tasks to assist workers – particularly dangerous or dispiriting drudge work. A good example is a warehouse automation system that performs parts picking.
Requirement 6: Measure Flexibility Return-on-Investment (ROI)
· If We Can Measure Quality, We can Measure Flexibility
We have made a lot of advances in measuring quality in recent years. The concept of driving down the number of defects is easy to understand. Measuring the success of a program that increases factory flexibility is a little trickier – it requires (as we said at the outset) defining our goals and how we measure success.
· Define What Success Means First – Before Investing in Technology Solutions
Start by having a clear understanding of your goals and success metrics – before writing a check for a shiny apple, whether it’s a new Production Planning software system, a new Enterprise Resource Planning (ERP) system, a whole slew of IoT sensors on the production line, or a Big Data Mining toolkit to delve into mounds of production data.
It’s not unheard of for these all-encompassing systems to make it harder to achieve your flexible production goals, so proceed cautiously by keeping people first, clearly communicating your goals, and measuring results.
· Calculate the Return on Investment (ROI) in Factory Flexibility
Establishing clear goals and metrics is a necessary step for calculating the return on investment (ROI) on flexible factor expenditures.
But a word of caution.
You will have to think carefully about how to accrue these costs, as many of them represent an investment in “potential.”
It’s similar to buying a fire extinguisher. You can book the expense as a cost of doing business, but if the fire extinguisher saves the factory from burning down in a fire, it’s much more valuable than its purchase price.
So too with investments in flexible factories. Some years you may have a hit product and maximize production on this most profitable line – diminishing the value in investing in flexibility during these good times. Yet, during other years, flexibility may help you save substantial sums by being able to switch to a different supplier (if your normal one goes out of business) without cutting production – or maybe you introduce several new products to bolster sales.
Take the Next Step with Formaspace, Your Partner for Flexible Manufacturing
If you can imagine it, we can build it – here at our factory headquarters in Austin, Texas.
Talk to your Formaspace Design Consultant today and find out why leading manufacturers, such as Apple, Dell Computer, Google, Oculus, SpaceX, and Toyota, choose Formaspace furniture solutions.