Looking for ways to jump-start your manufacturing facility to make it more innovative and competitive? Process improvement alone is not enough. The key lies in creating a manufacturing company culture that’s engaged, empowered, and ready to take on the world — to win.
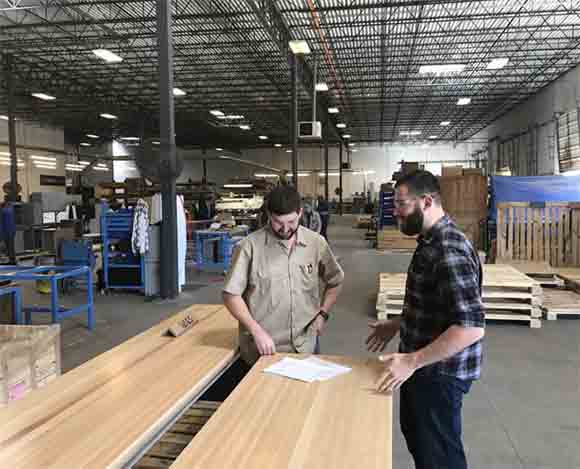
At a time when American manufacturing is poised to make a major comeback, there remains a sticking point — a looming labor shortage as many high-paid, high-tech manufacturing jobs go unfilled. We’ve written previously about the challenges manufacturing companies face in attracting the next generation of workers. In the article, we touched on the importance of improving STEM training as well as the need to create deeper ties between industry and the pool of potential workers through apprenticeship programs.
But what about improving manufacturing company culture? Isn’t that also part of the solution?
We live in a time when workers choosing a career have unprecedented visibility into a company’s culture. Social media and employer reviewing websites, such as Glassdoor, provide direct access to employee commentary of what goes on inside their workplace — at its best, and at its worst. Like Yelp restaurant reviews, savvy readers will ignore the most damning as well as the most effusive, praising reviews as they are likely to be biased. However, the bottom line is clear: if you are looking for a new career, it’s plain to see from review websites and news reports that while many professions are busy changing their office culture to make it more welcoming, accommodating, and flexible for workers, most manufacturing companies seem stuck in the past.
Workers at manufacturing companies are noticing.
According to a recent Gallup survey, the State of the American Workplace, workers at manufacturing companies are the least engaged in their work — a full 8 percentage points behind all other industry sectors. Gallup consultants point out that manufacturing workers want what they perceive their friends and family working in other industries have: more empowerment and flexibility at work, including the ability to set flex-time hours and customize their job role to better fit their needs.
Maybe it’s time to take a step back and take a look at the big picture. What aspects of manufacturing company culture needs to change for careers in manufacturing to be seen as desirable and worthwhile? Which manufacturing culture changes could help make American manufacturing more competitive in innovation, quality, and efficiency? What can be done to reduce the cost of employee turnover? And most importantly of all, how do you go about making these beneficial changes to the manufacturing culture without causing major disruption?
Here are seven recommendations you can use to change your company culture:
1. Get Started With “Keep It Simple Stupid” (KISS) Management Strategies
If you want to change the culture in your manufacturing facility for the better, it can be overwhelming to decide where to start. Don’t reinvent the wheel. Use simple, proven methods to get started.
Well-known manufacturing management techniques, such as 5S, Kaizen, and the Toyota Way, inspired by Toyota (and other Japanese firms) are good places to start. Not only do they help you get organized, they can often provide quick, positive results that will help inspire confidence in making further changes.
These programs will not only help you clean up your facilities, making them more efficient, they can also engage employees and make them take more pride in their work. But the benefits of 5S and Kaizen principles go beyond an initial organizational cleanup: these techniques can help provide you and your workers with useful visual information that will help everyone understand production bottlenecks and other trouble spots. It’s an important first step in a cultural shift toward shared responsibility for production.
Gray Engineering consultants have given us a good, real-world example: As Marty Bryant moved from Toyota to become head of operations at an automotive supplier, he realized his new employer had invested heavily in technology to gather metrics — but the information never surfaced on a daily basis to make a difference on the shop floor. The solution: a highly-visible white-board strategically placed for everyone (from the CEO to the shop worker) to see — with color coding that highlights which production processes were on track, behind plan, or stalled completely. No more hiding bad news inside weekly KPI reports!
Not sure if you are ready to tackle this yourself? Why not call on our experienced Formaspace Consultants? Our Rapid Plant Assessment program will help you quickly pinpoint problematic areas in your factory operations, such as inefficient material handling and poor workflow. Their recommendations can help you put workers first by creating efficient processes from materials handling to the manufacturing floor to the warehouse shipping and packing stations.
2. Change Work Attitudes from “It’s not my job” to “It IS my Job”
Good employees want to do good, quality work that makes a difference. But oftentimes, something gets in the way.
When workers no longer feel that their contributions can make a difference, they can feel overwhelmed by a feeling that things are out of their control. As a defensive mechanism, they often retreat into their “shell” to focus on their specific job task — and no more. This can lead to destructive conflicts to adjudicate what are “their” responsibilities versus what are the responsibilities of “others.”
Research by the consulting company PwC shows this problem surfaces across all industry sectors, not just manufacturing. In their 2017 Employee Engagement Landscape Study, the most common workplace obstacle reported by 33% of workers was, “Doing work for others that is not part of my job.” Rounding out the top five employee complaints were:
- Being included in meetings unnecessarily 24%
- Paperwork (e.g., reports) 23%
- Lack of clear priorities 21%
- Lack of clarity about the decision-making process 21%
So when you hear the phrase, “it’s not my job,” you have a problem on your hands. Your employee (who likely represents many others at your company) isn’t feeling they are part of the solution. Instead, they are saying they lack ownership and empowerment, the very characteristics needed to create a culture of quality and innovation.
How can you change the culture from “it’s not my job” to “it IS my job?”
This is a tough problem because it touches on so many aspects of the business. But we recommend starting out by promoting the role of quality and what it means for your workers — from customer satisfaction to the health of the business.
In a Harvard Business Review article Creating a Culture of Quality, authors Ashwin Srinivasan and Bryan Kurey contend that implementing these four principles can make the difference:
- Leaders need to “walk the walk” on quality, not just pay lip-service.
- Workers need to hear the importance from respected sources in ways that appear to them personally.
- Find key influencers respected by the worker community who can use peer influence to promote the role of quality among team members.
- Ensure workers know that they are empowered to speak up and make changes to improve quality.
3. Create Clear Pathways for Job Advancement, Education, and Training
Are you having trouble attracting a talented workforce? You are not the only one.
The manufacturing industry’s ongoing recruitment problem is made worse by the high cost of employee turnover.
Talent recruiter Mike Morrow, writing in Industry Week, laments the poor state of the manufacturing industry’s ability to retain quality employees or to develop talent within their ranks. He says: “Let’s face it — when graduating engineers have a choice between a forward-thinking culture and a stodgy traditional manufacturing culture, their choice is easy.” In Morrow’s view, the problem is made worse due to poor internal employee development — in fact, about 75% of his manufacturing clients have failed to develop any high-potential, internal candidates at the five-year mark that can advance to the next level of job responsibility.
The solution?
Be proactive about communicating the exciting challenges and rewards that a career in manufacturing can offer: in a world of data-driven design that’s powering the Internet of Things, self-driving cars, and 3D printed products (from rocket motors to prosthetic surgical implants), nothing could be more interesting than taking part in the fast-paced world of product development and manufacturing.
Crucially, you need to back that promise up with continued training and cross-training within your workforce. Each employee needs to know how they can learn on the job, and that they can learn from other jobs as well. Not only will this help employees become more knowledgeable and engaged, it will help break down silos within the business. Create cross-functional teams to solve problems: get engineers, shop mechanics, and business developers working together. Challenge people to stretch to meet new goals and come up with new innovative solutions.
Here at Formaspace, we believe in developing and promoting talent from within. A great example is our new Production Manager, Cody Adams, who moved up from an entry-level position on the shop floor to a management position overseeing production workflow in the manufacturing department. Adams has been busy leading efforts to improve workflow improvements using Kaizen principles and expects to increase labor efficiency by 15% in 2018. Adams and other supervisor employees also sit at the management table during weekly planning meetings, making sure that manufacturing concerns are front and center in the company’s overall decision-making process.
Finally, take the time to understand the psychology of those working for you and how they view their careers. The PwC report mentioned earlier identifies three key stages of the idealized work experience progression: Foundational, Developing, and Distinctive. It’s a read that’s worth your time.
4. Implement Software Systems and Data Collection Wisely
Data is the heartbeat of everything that is happening in business today: The Internet collects data from consumers, smart sensors in products collect data from installations, big data software processes it, artificial intelligence helps interpret it. Manufacturing companies who understand this paradigm shift are moving ahead, prospering from major shifts in consumer demand.
As a result, manufacturing companies have two parallel challenges that come from the new world of pervasive data: first, how to retool their manufactured goods to provide the services that customers want in a world of instant communication, and, second, how to create open lines of communication within their organizations needed to instill transparency and trust. And to make it more complicated, all this has to be done without compromising customer data at the hands of Internet thieves or revealing trade secrets to the prying eyes of industrial espionage spies.
This is a tremendous cultural challenge on many fronts. Integrating what are essentially teams of software developers into a manufacturing operation that had one before is challenging enough, but it’s just the start. Leveraging production and customer data by plugging it into process mining tools is just one example of what can be done with pervasive data.
Our recommendation: establish cross-functional teams to tackle these important issues head-on. Don’t keep workers in the dark about the inevitable changes that will come from automation and robots. Make them part of the process, and show them a viable career path where their contributions will become more important as part of these ongoing technology-driven transformations.
5. Make Sure Everyone Knows What is Going On… Except Your Competitors
Today’s companies have an unprecedented number of ways to transmit information, from Slack to Snapchat, from email to Instagram, but the question remains — are we really communicating effectively within our organizations?
It’s easy to conclude if you have a vigorous outbound social media campaign that your workforce will be up to speed on company news. Yet that’s likely to prove insufficient for creating a culture of trust and transparency. In fact, social media execs themselves are eschewing their own products — in the ultimate refutation of the “eat your own dogfood” business principle, as reported in this article “Never Get High On Your Own Supply — Why Social Media Bosses Don’t Use Social Media.”
What is needed?
In our view, old-fashioned face-to-face communication is a key part of the solution, even if it’s done virtually over a telepresence conference table.*
As part of your communications program, you and your leadership team need to:
- Show by your actions that you live up to your company’s values.
- Communicate clearly to develop transparency and trust.
- Recognize and celebrate individual and collective successes.
Remember that communication is an ongoing effort that’s not limited to the boardroom and the conference center. Creating collaborative spaces where employees can meet and work on projects together is equally important.
Toyota’s North America CEO Jim Lentz is a believer. In an interview in the Dallas Business Journal, Lentz explained that their brand new LEED-certified headquarters in Plano, Texas has dedicated a full 50% of the floor plate to collaboration spaces (up from 20% in their old headquarters in Torrance, California).
“The collaborative piece is way beyond conference rooms,” according to Lentz. “It may be a couch and a couple of chairs near a stairwell. It may be some highboys where people can bring their laptops and sit down and work together… It’s much more of an interactive space,” explained Lentz. “We are going to try to be a catalyst for getting people out of their offices, not emailing back and forth to each other, but actually sitting down, collaborating and communicating because we believe that’s where innovation takes place.”
6. Make Wellness, Safety and Security Mainstream, Not a “Once in a While” Topic
More and more leading manufacturing companies are incorporating the type of health and wellness programs for their employees that once were the domain of Silicon Valley software companies. For example, three companies ranked on Fortune magazine’s list of Great Workplaces in Manufacturing and Production feature extensive health and wellness benefits:
- #4 Ranked Arthrex: This $1.5 billion revenue Naples, Florida maker of surgical products covers 100% of worker health and dental benefits, reimburses gym memberships, and provides on-site medical facilities.
- #6 Ranked EOG Resources: This $144.9 billion revenue Houston-based oil exploration company promotes well-being with fitness reimbursements of up to $300 per year.
- #13 Ranked FONA International: This $78 million revenue Geneva, Illinois provider of food additives and flavorings helps its employees keep mentally and physically fit with free yoga and exercise classes.
Ergonomic, well-suited furniture can promote good health and help prevent injury on the job as well. Formaspace offers a full line of custom, adjustable workstations and desks, as well as specialized furniture solutions, such as ESD solutions for electronics manufacturing and customized packing stations for your warehouse and shipping operations — all designed to fit different-sized individuals comfortably and securely. Our line of Sit-to-Stand furniture features built-in motors that can raise and lower the work surface throughout the day at the touch of a button — providing increasing circulation for improved cardiovascular health.
Safety at work is a special concern in manufacturing facilities where lifting objects improperly or tripping and falling are major causes of accidents on the job. Speak with your Formaspace Design Consult to learn how custom lifts and movable surfaces can reduce the risk of injury at work.
In our view, it’s important to change the manufacturing culture from viewing health, wellness, and safety as separate, “once in a while” topics — instead, it should be part of your everyday operations.
7. Break Down Barriers for Better Results by Establishing a Culture of Respect
Here are some questions to ask yourself:
- Do your engineers work within a few steps of the production line?
- Do your managers walk the line on the second or third shift of the day, greeting people by name?
- Does your executive leadership isolate itself with separate dining facilities?
- Do your employees ever “walk in the shoes” of your customers to see things from their perspective?
- Are women leaving the company or turning down interviews to join your team?
- Do individuals feel unwelcome or shunned because of their background or “just because they are different?”
What do these questions have in common? They are measures of the level of respect that your company shows to its workers, and, by extension, to your customers.
Do not forget: Respect is at the foundation of a healthy company culture.
Why?
Without respect, people begin to feel unwanted, detached, isolated, or worse, embarrassed or even humiliated — one of the strongest, most powerful and most hurtful emotions of all. To be blunt, it’s often the underlying cause of serious disruptions — even capable of causing workplace violence.
Take the time to build a culture of respect in the workplace that welcomes everyone.
What Makes a Company More Innovative?
Every company is looking for the “secret sauce” that will help them innovate and outperform the competition.
Each of the seven recommendations we’ve provided can have a positive impact on improving the manufacturing culture at your facility.
In no way can this be the ultimate comprehensive list of action items. For example, we haven’t had room to mention how Google sets aside a small percentage of time for its engineers to experiment on ideas they think have promise, or how Houston oil and gas engineers with expertise in hydraulic pumps are sharing expertise with heart doctors seeking ways to improve heart surgery outcomes.
But we will conclude with some thoughts on innovation from Alan Murray, who wrote the “The Wall Street Journal Guide to Management.” Murray’s message for executive leaders comes from the book, “Blue Ocean Strategy,” by W. Chan Kim and Renee Mauborgne:
- Because you can’t change everything at once, try to change those people who have disproportionate influence within your organization. Celebrate their successes to get the message across that this is important for the company.
- Make people eat their own dog food. Do like New York Police Commissioner Bill Bratton did in the 1990s, who (along with his leadership team) rode the subways day and night to experience firsthand why New Yorkers were so frightened of the transit system.
- Focus first on areas where improvement will result in large change; avoid areas that require many resources but won’t have much impact.
- Appoint a point person, or “consigliere” who can bird dog the fight on your behalf by building coalitions, as well as creating and implementing strategies for change.
Want to learn more about changing the culture at your manufacturing facility? Talk to your Formaspace Design Consultant. Tap into our experience of working for leading Fortune 100 manufacturing companies to make your facility a more competitive, productive, and innovative place to work. Just fill out the quick contact form below to get started.